Scanning shall be done at the rate of maximum 2 feet per minute. the particle count exceeds clean room specification limits. Most contamination-sensitive environments in a pharmaceutical industry such as dust-free hoods require laminar flow because it predictably sweeps particles in a uniform direction, from the cleanest area under the hood. SOP for Operation, Cleaning, and Monitoring of Bio-Safety Cabinet. Different membranes should be used in different systems depending on their characteristics. The Laminar Flow Cabinet is maintained a constant positive air pressure to prevent the intrusion of contaminated room air. The main principal in the RLAF is "A negative pressure inside the booth prevents the escape of fine powder from the work area towards the external environment.Downward airflow provides full protection to operator and product". 5.2.16 After cleaning & air drying put the cleaned filters in clean polythene bags and re-fix the filters. Product Details: A Reverse Laminar Air Flow -also called a Dispensing Booth and Sampling BoothReverse Laminar Air Flow is designed to provide Class 100 working environment at rest with built in scavenging system to ensure product, operator as well as surrounding environment protection. The key difference between laminar flow hoods and reverse laminar flow hoods is that the former protects items on the work surface while the latter protects operators. 4.6.2 Check that following tests are passing before starting airborne particle count: 4.6.3 Particle count shall be checked at 3 locations per filter for RLAF and LAF and 1 location per filterfor Dynamic Pass Box at the height of the work activity. Comments having links would not be published. It is a dynamic barrier of HEPA-filtered unidirectional air flow to move particles away from the filling/closing area. A platform lead by pharmaceutical specialists to grow-up pharmaceutical professionals with scientific and technical knowledge. Holiday What is the differences between LAF & RLAF? Greenville, SC The air system should be provided with appropriate filters such as HEPA for grades A, B, and C. (b) The guidance given for the maximum permitted number of particles in the at rest condition corresponds approximately to the US Federal Standard 209E and the ISO classifications as follows: grades A and B correspond with class 100, M 3.5, ISO 5; grade C with class 10000, M 5.5, ISO 7 and grade D with class 100000, M 6.5, ISO 8. PAO: Poly alpha olefin 4.3.9 Scanning shall be performed over the entire downstream face of each filter, the perimeter of each filter, the seal between the filter frame and the grid structure. Check the magnelic gauge, the needle should be at zero. Begin at the back of the unit and work your way to the front. A few differences between a LIF and RRIF are as follows: Unlike an RRIF, you can only transfer locked-in pension funds into a LIF; There's a maximum cap on the maximum amount you can withdraw from a LIF per year; In Newfoundland and Labrador, LIFs must be converted and used to purchase a life annuity when you turn 80. The cookie is used to store the user consent for the cookies in the category "Other. 46677. . This is why such filters are a critical feature in bigger cleanrooms. Weblink https://pharmastate.com/ These criteria are intended to reduce the risk of microbiological, particle, and pyrogen contamination. difference between laf and rlaf in pharma. Filling, Processing and Packaging, Particle level (> 0.5 m) less than 3,520 particles/m. This is what we call a Clean Non-Classified (CNC) area. Some operations, such as the manufacturing of non-sterile pharmaceuticals, do not automatically require a cleanroom, whereas sterile drugs necessarily do. 6.3 Record of FBD filter cleaning Annexure -3 Like the Grade C cleanroom of a GMP facility, the Grade D area is used to perform less critical steps in manufacturing sterile drugs.
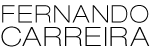